The Core Kanban Principles and Practices
- 1. What Is Kanban? The Ultimate Guide to Kanban Methodology
- 2. The Core Kanban Principles and Practices
- 3. What Is a Kanban Board? Examples and Usage Guide
- 4. Everything You Need to Know About Kanban Cards
- 5. Ultimate List of Kanban Tools and Software
- 6. Practical Kanban Templates and Examples
- 7. The Complete Guide to Personal Kanban
- 8. Kanban WIP - Work In Progress Limits Explained
- 9. What Is a Kanban Retrospective Meeting?
- 10. Kanban vs. Scrum Comparison Guide
- 11. Glossary of Kanban Project Management Terms
- 12. FAQs
- 1. What Is Kanban? The Ultimate Guide to Kanban Methodology
- 2. The Core Kanban Principles and Practices
- 3. What Is a Kanban Board? Examples and Usage Guide
- 4. Everything You Need to Know About Kanban Cards
- 5. Ultimate List of Kanban Tools and Software
- 6. Practical Kanban Templates and Examples
- 7. The Complete Guide to Personal Kanban
- 8. Kanban WIP - Work In Progress Limits Explained
- 9. What Is a Kanban Retrospective Meeting?
- 10. Kanban vs. Scrum Comparison Guide
- 11. Glossary of Kanban Project Management Terms
- 12. FAQs
Kanban principles and practices today are different from those developed in the 1940s when the methodology was originally developed. Over the decades, advances in technology and innovation have transformed industries meaning that Kanban’s just-in-time and pull systems have expanded beyond manufacturing. The digital era has created new markets altogether, including ones powered by software running on computers and online.
The change has been cultural too, with organizations investing more in people, giving them the tools and environments for them to be more productive. Because of this Kanban has been adapted to fit a broader context: different industries, technologies, types of organizations, and working practices.
Taiichi Ohno, who is considered the father of Kanban, focused much of his work on limiting waste, which was a major issue in car manufacturing plants at the time. Today his "Seven Wastes" model remains relevant but only in certain industries. That said, his ideas and principles have spilled outside manufacturing. Ohno’s ideas have influenced the service industry as well as disciplines such as sales, marketing, and customer care.
Today, one of the main reference points for Kanban is David J. Anderson, a management consultant and pioneer of the Kanban method and a number of related frameworks. His book, Kanban: Successful Evolutionary Change for Your Technology Business, is regarded as one of the best resources on Kanban. In the book, Anderson covers five core properties that characterize successful Kanban implementations — a list that has since grown into a more comprehensive set of 4 principles of Kanban and 6 Kanban practices.
The 4 principles of Kanban
If you’re familiar with the Agile manifesto principles these will look familiar to you:
- Start with what you do now
- Agree to pursue incremental, evolutionary change
- Respect the current process, roles, responsibilities, and titles
- Encourage acts of leadership at all levels in your organization
The first one is particularly significant as it is a key requirement now as it was sixty years ago. Kanban needs to sit on top of existing processes and not replace them. It would have been too disruptive and costly to change the modus operandi altogether. Instead, Kanban was designed to streamline existing systems.
Let’s look at each of the 4 principles of Kanban in more detail:
1. Start with what you do now
As mentioned, Kanban acts like a ‘power-up’ that recognizes value where it exists and addresses issues that hinder processes and outcomes. Every aspect is considered: workflows, roles, responsibilities, titles, communications, and any other component of the process.
This principle is a useful selling point for Kanban too. It becomes easier to justify implementation costs when you can clearly present the benefits: minimal disruption, maximizing efficiencies, and cost savings.
Change management professionals will highlight these as part of a discovery phase at the start of a project, quantifying ROI over time as well as the additional transparency Kanban delivers. It becomes easier working with existing project managers too, as they will not feel threatened by changes coming their way.
2. Agree to pursue incremental, evolutionary change
This principle relates closely to the first one and is also a key one in Agile and Scrum. Kanban’s model is less time-based than the latter, which organizes work in sprints. The notion of continuous development is shared by both, as is delivering change in small, manageable increments.
Kanban recognizes that big changes are hard to implement and are likely to meet resistance on multiple fronts. Senior management is typically concerned about spiraling costs while project teams feel that changes to their working practices may slow them down and affect quality.
3. Respect the current process, roles, responsibilities, titles
This is another principle that reinforces the idea that Kanban is not a disrupting force taking over established operational models. In this respect, Kanban is more of a compromise, gently improving legacy processes without changing the underlying framework.
The objective is to gain support for Kanban in an environment where people may have a vested interest in established practices. This is particularly true for larger organizations where change is slower and harder to achieve.
4. Encourage acts of leadership at all levels in your organization
Kanban recognizes the power of collaboration but also allows anyone to take ownership of an issue and address it. Armed with strong justification and data to back up an argument, anyone should be able to take action.
By promoting a culture of safety, as David J. Anderson refers to it, Kanban empowers team members to lead, take risks and grow professionally.
Overview of the 6 Kanban practices
While there are some overlaps with other Agile frameworks, Kanban is based on pull systems which allow you to start work where there is demand for a deliverable. As opposed to a time-based approach like Scrum, where sprints and events follow strict schedules.
The 6 Kanban practices are:
1. Visualize (the work, the workflow, and the business risks)
Most people involved in project management are familiar with Kanban boards, whether used in Scrum meetings or online task management. Think of these as dashboards for project work where the intention is to give visibility to as much information as possible in a format that is easy to understand.
In its simplest form a Kanban board features three stages:
- To-Do
- In Progress
- Completed
You can add more stages to best serve a particular process too. For example, adding a ‘Review’ stage between In Progress and Done.
The sequence across the stages is referred to as the workflow. It starts with discovery activities (eg. a request being made) and ends with delivery — the feature that has been completed and delivered back to the customer.
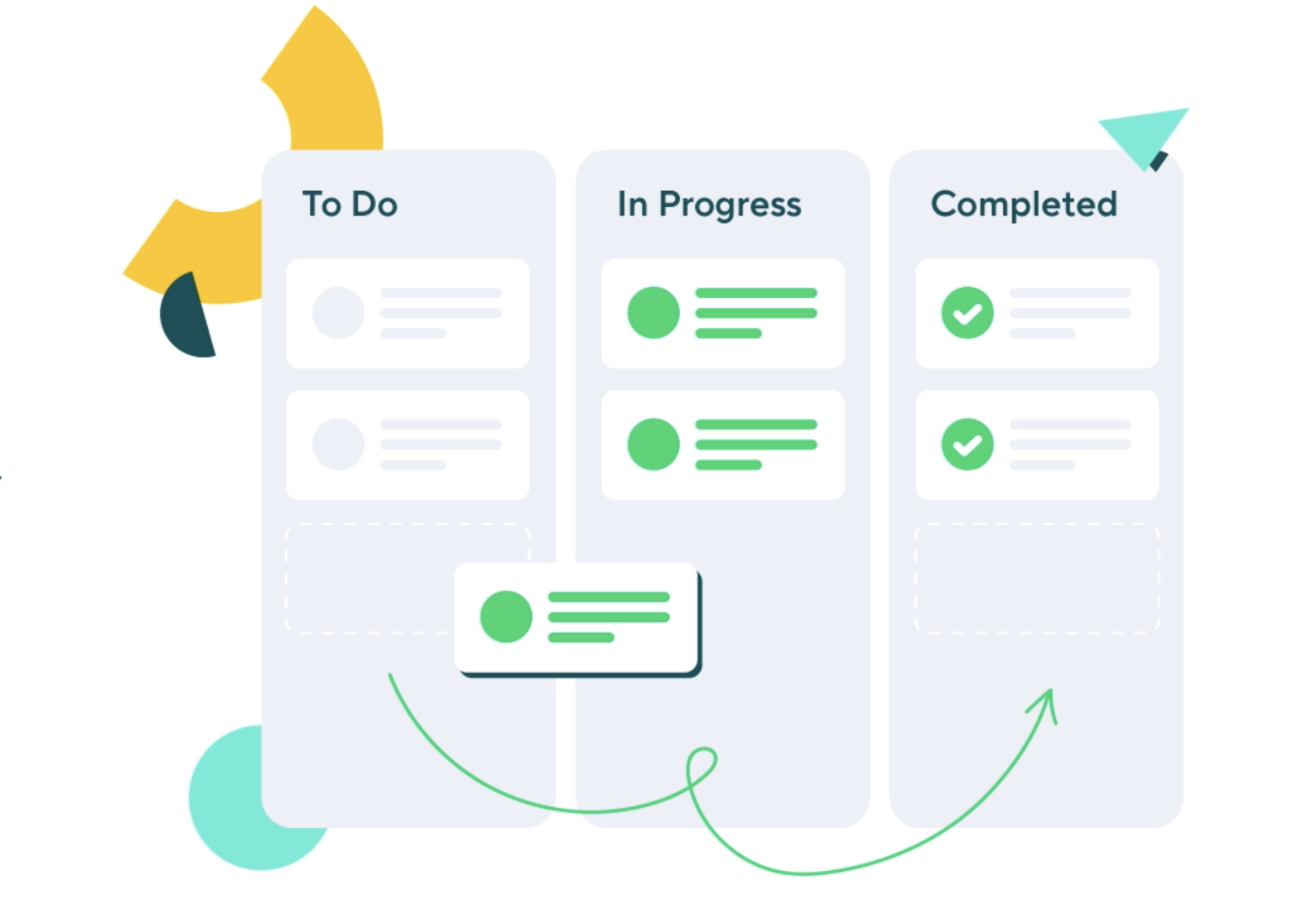
In the Kanban system, there are three items that need to be visualized. These are the work, workflow, and business risks.
Work - Each card represents individual tasks. You can quickly understand what stage they are in by looking at the column. A quick glance at the board helps you understand how the project as a whole is progressing.
Workflow - These are represented by different stages, from left to right on a Kanban board.
Business risks - You may need to look at details for each card to determine business risks but there often are visual cues. For example, if more cards than expected are listed in the “Doing” or “In Progress” stage there may be a bottleneck slowing down work.
Whether using an online board or a paper-based system, color codes, tags, and labeling are useful to highlight key information.
2. Limit Work-In-Progress (WIP)
Limiting WIP ensures that at any point in time there is never too much or too little work to do. You want to have just the right amount of cards on a Kanban board that can be handled by resources available.
This is achieved by implementing a pull system where new work is only ‘pulled’ in when there is enough capacity to handle it. For this to work, limits to WIP need to be set and adjusted. For example, to have a team of 20 engineers and operators build 10 cars a week.
3. Manage flow
Flow refers to the movement of work items across stages of a process, as represented by cards on a Kanban board.
The responsibility lies with the project manager (or whoever is given ownership of the process). He/she needs to keep the workflow moving fast while keeping an eye on blocks, bottlenecks, and risks.
Tracking speed and smoothness of flow allows leadership to determine how efficient a process is and how that affects the bottom line. As a metric, it isn’t dissimilar to Velocity in Scrum, which is one of the more important ones.
4. Make policies explicit
By having an explicit understanding of issues, operations, and rules, discussions become more rational and objective. These need to be documented and shared across the project team. The intention is to prevent emotion and subjective views from seeping into the decision process.
5. Implement feedback loops
Feedback and continuous improvements are critical for Kanban as they are for other Agile frameworks. In Kanban feedback is gathered at different stages of a project: during meetings or at delivery, operational and risk reviews.
The frequency and format of feedback depend on what has been already established by the Project Office. Any gaps are filled as Kanban identifies them.
6. Improve collaboratively, evolve experimentally
In Kanban, collaboration and experimentation go hand in hand as long as there is clarity and consensus on how to approach work and issues.
In his book, David J. Anderson talks about teams having a shared comprehension of problems and suggests the adoption of a model to be able to predict the effect of change. These include:
- The Theory of Constraints
- The Theory of Profound Knowledge
- The Lean Economic Model
By using a proven model it becomes easier to measure outcomes, including the changes leading to them. This helps retain clarity and mitigate risks.